Grimshaw was appointed by the University of Southampton in 2009 to develop a long-term master plan for its 10-acre Boldrewood site. The brief was to deliver state-of-the-art buildings and facilities that would place the university at the forefront of engineering excellence, broaden collaborations with other leading institutions and business, and cement Southampton as the UK’s home of maritime research. Over the subsequent ten years, six individual building projects have been delivered to create the Boldrewood Innovation Campus, a world-leading hub for innovation, business and education.
The Boldrewood Campus is the UK’s largest University/Industry partnership and the recently delivered National Infrastructure Laboratory forms a significant part of the UK Collaboratorium for Research on Infrastructure and Cities (UKCRIC) initiative Grimshaw’s ambitious masterplan combines the National Infrastructure Laboratory, the Engineering Centre of Excellence, the Hydro-Sciences Building and Lloyd’s Register’s Global Technology Centre, as one world-class research hub. The £140m scheme also delivered a multi-storey carpark, refurbished existing buildings and implemented a coherent signage and wayfinding strategy.
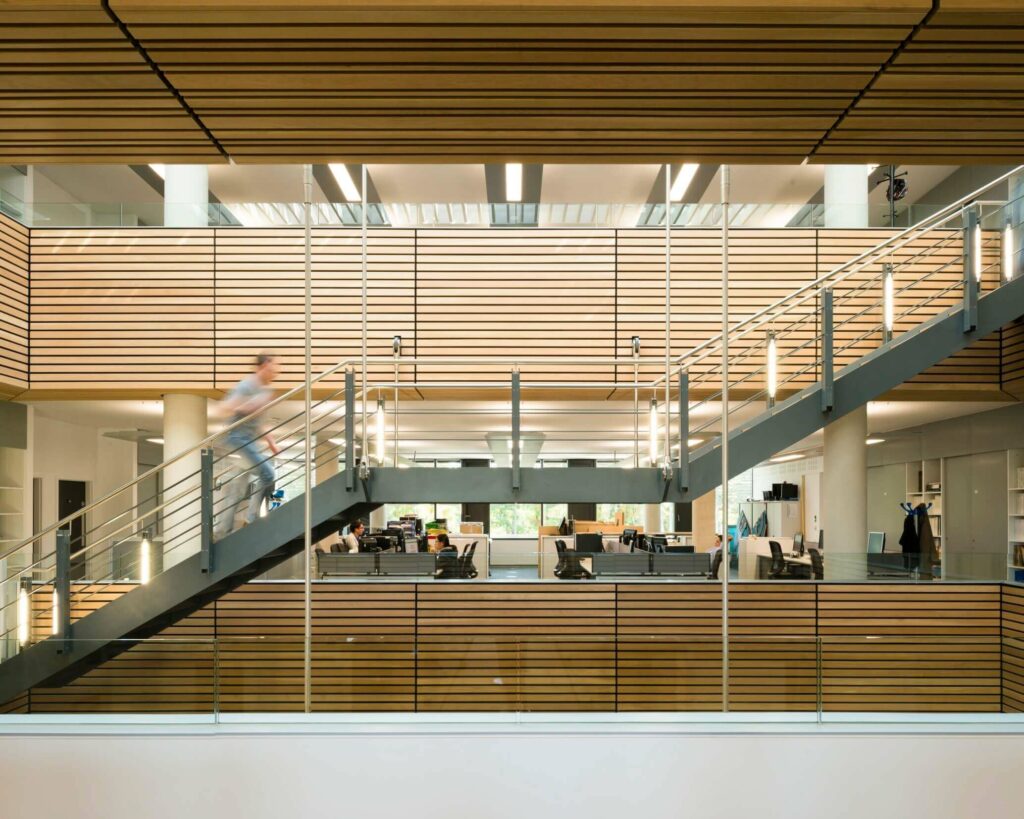
The rare chance to deliver both the masterplan and all buildings within it provided the opportunity to develop a ‘family of buildings’, and create a visual coherence that reinforces a campus identity and enhances the user experience.
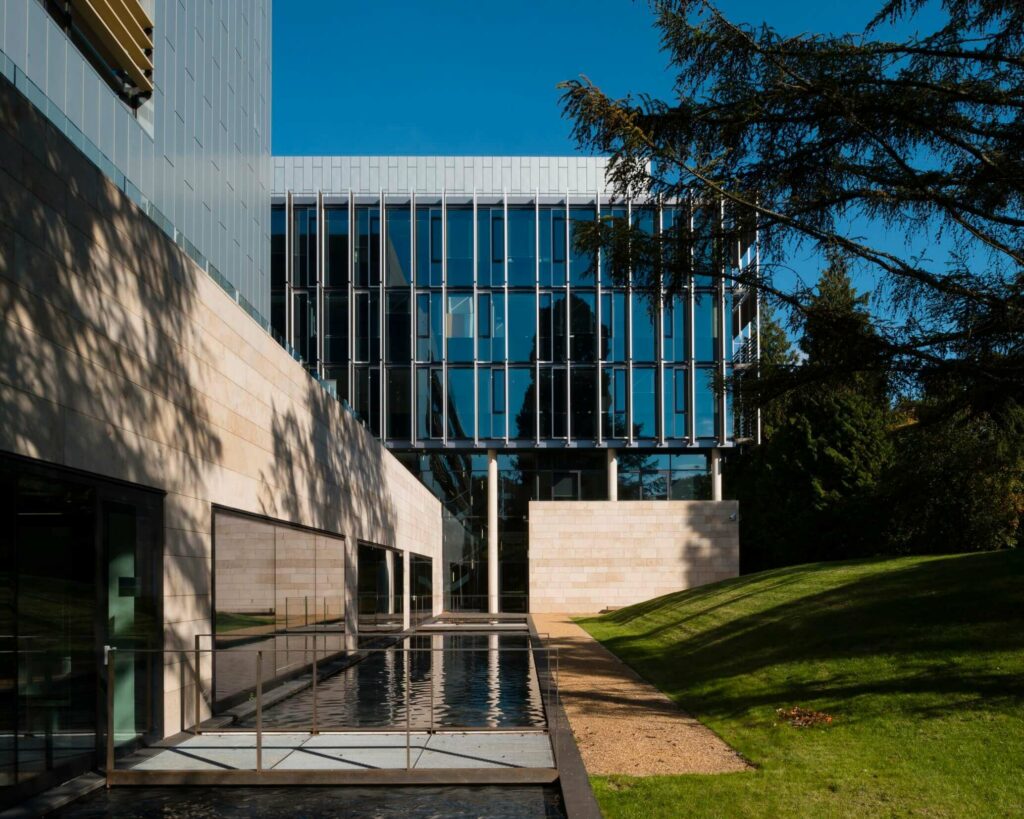
The rare chance to deliver both the masterplan and all buildings within it provided the opportunity to develop a ‘family of buildings’, and create a visual coherence that reinforces a campus identity and enhances the user experience. The Boldrewood site’s urban parkland setting contained mature surviving trees from a Victorian arboretum, which were incorporated into the design to provide a green border to the development that complements its leafy residential surroundings and suggests a seamless transition between the campus and the local neighbourhood.
Refined and understated, the new buildings derive their character from crisp and simple detailing and draw from a shared palette of materials ― Jura limestone, zinc cassette panels, terracotta baguettes, anodised aluminium, glass and cedar boarding. The buildings were carefully integrated into the existing landscape to respect the parkland setting and harness the positive impact that biophilic design has on health and wellbeing.
The central green quadrant of the campus is the external focal point, while the entrances to all buildings face a sloping lawn in the centre of the open space. The landscape design takes into consideration views out from all workstations, pedestrian links between buildings, and offers a myriad of spaces to reflect, relax and socialise.
Responding to the interdisciplinary collaboration at the heart of the university’s brief, the campus’ striking array of facilities feature a range and proximity that enables crossover between different areas of study and research, as well interaction with external business stakeholders. The Engineering Centre of Excellence features teaching laboratories on the lower floor, seminar and informal learning spaces and a café on the ground floor, and PhD office accommodation across three floors and an atrium. It shares a podium with Lloyd’s Register’s Global Technology Centre, which houses a Maritime Institute designed specifically for projects shared between Lloyd’s and the University.
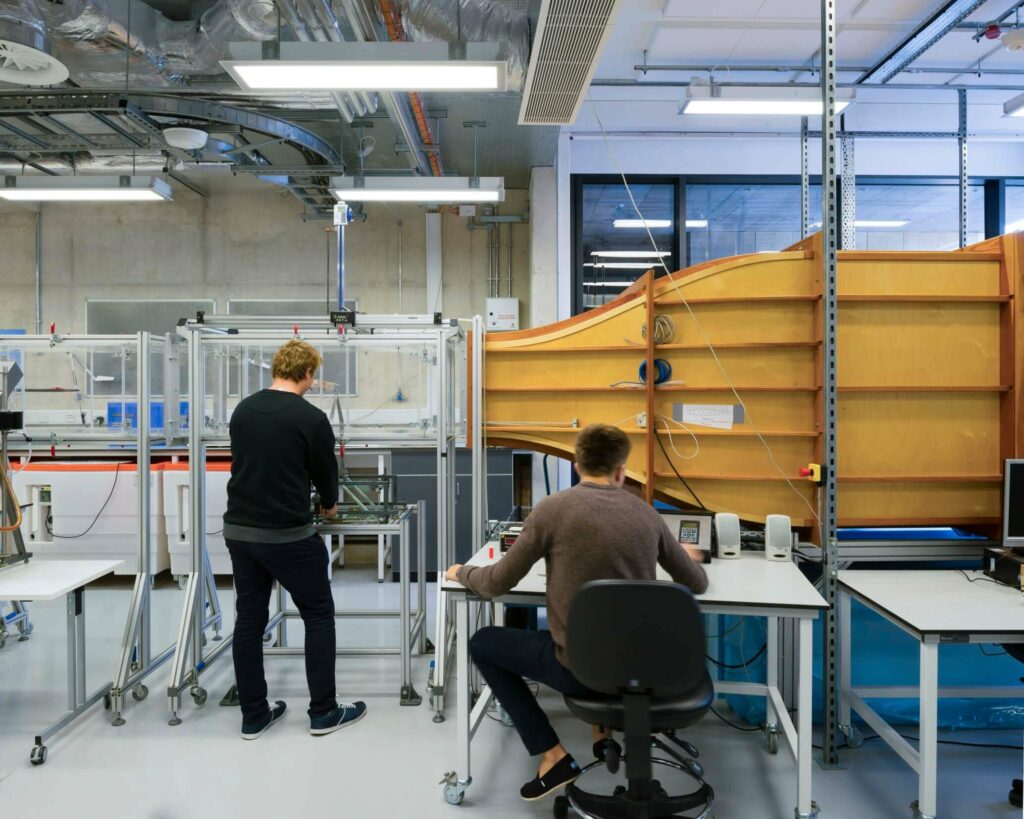
The National Infrastructure Laboratory combines heavy-duty and flexible laboratories, including a 30x15m multi-axial strong floor and centrifuge, open-plan offices on the upper floors and column-free informal learning space at the ground floor that is open to the public. The Hydro-Sciences building is developed around a 138m long towing tank and contains a double-height anechoic chamber and wet fluid testing laboratories, seminar rooms, open-plan offices and breakout spaces.
All facilities have, where possible, been designed to enable a flexible approach to their current and future use. Partition and non-structural walls allow easy adjustment, while informal teaching and learning spaces can be opened up to café and break out spaces to maximise theirs functionally.
The flexibility of spaces and potential for their adaptive future use is one of a number of ways the campus was designed to achieve a high standard of sustainability. To promote energy efficiency, solar gain is minimised through approximate solar shading and a glazing system that manages thermal gain, daylight and glare through a combination of natural and automating ventilation. In maximizing natural daylight and ventilation, it has been possible to create a comfortable, low energy environment.
A mixed-mode system, complemented by louvres on top of each atrium, encourages natural ventilation for most of the year, while at night the exposed concrete soffits are cooled, extending the period during which the building is naturally ventilated. Mechanical systems only operate in extremes of external temperatures, ensuring significantly less energy is used. The building’s systems were designed to accommodate temperatures both below and in excess of standard design criteria to ensure it is resilient to changes in climate.
A mixed-mode system, complemented by louvres on top of each atrium, encourages natural ventilation for most of the year, while at night the exposed concrete soffits are cooled, extending the period during which the building is naturally ventilated.
To further reduce energy consumption, the buildings incorporate an array of state-of-the-art lighting control technologies, including automatic dimming of fittings as natural daylighting increases, and absence detection to switch off lights when spaces are unoccupied. A large proportion of the building has LED lighting rafts that also help to reduce energy consumption. Stairs were placed in each building to encourage occupant use and minimise the requirement for lifts, promoting fitness while reducing energy consumption.
The campus is powered via infrastructure that connects the buildings to a combined heat and power district heating main. A CHP energy centre has been implemented as part of the National Infrastructure Laboratory, reducing energy consumption profiles while ensuring the highest levels of efficiency. Although laboratories often consume high levels of energy, all campus buildings were tested upon completion and have proven to outperform the standards set by the Building Regulation, as well as meeting and exceeding their targeted BREEAM requirements. This minimises the buildings’ impact on the environment and significantly reduces their annual running costs.

A sustainable approach to construction by contractor Wates ensured that local labour and fabrication were used wherever possible to minimise the carbon footprint of the building process. An example of this is the National Infrastructure Laboratory’s cantilevering steel stair, which was assembled locally at AW Jeffreys steel workshop in Southampton. Sustainable materials such as timber were used internally and externally, and a specification for high contents of recycled aggregates for all concrete was used.
Before the delivery of the entire master plan was completed, the excellence of Grimshaw’s design was already being recognised, with the project winning a RIBA South Award 2016 and a 2017 Civic Trust Award.
Completion of the campus ahead of our 2020 target is the result of a tremendous team effort of which Grimshaw has played an absolutely pivotal part. The completed campus has transitioned from leaky, high maintenance, low satisfaction place of brutal endurance to a simply stunning collection of buildings and landscaped spaces which exude design quality. Whilst it has been at times a difficult journey, we were very lucky to have a team that consistently pulled together in a positive way. We are delighted with the end result.
Kevin Monaghan,
The University of Southampton’s Executive Director of Estates and Facilities